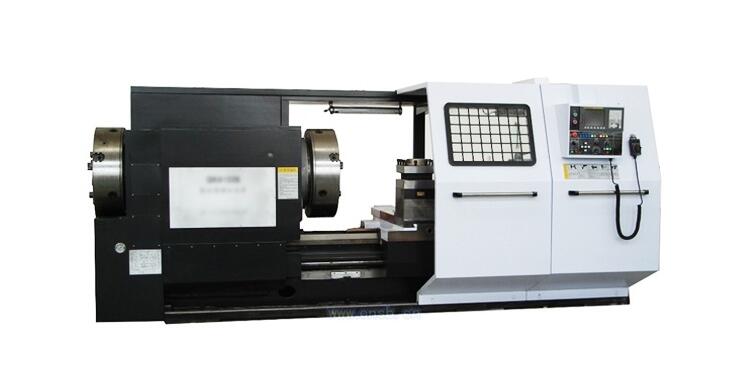
CNC technology is digital program control CNC machine to achieve automatic work technology. It is widely used in the field of machinery manufacturing and automation, better solve the multi-species, small batch and complex parts processing and production process automation. With the rapid development of computer and automatic control technology, numerical control technology has been widely used in CNC machine tools, robots and all kinds of mechanical and electrical integration equipment. At the same time, the rapid development of social economy, numerical control devices and CNC machinery requirements in theory and application of rapid development and improvement.
Servo system is an important part of CNC machine tools, CNC machine tool accuracy and speed indicators are often determined by the servo system. With the development of technology, high-precision, high-performance AC servo servo system has become a new trend.
1. Overview for it :
CNC lathes, also known as CNC lathes, that is, computer numerical control lathe, is currently the largest domestic use, the most extensive coverage of a CNC machine tools, generally by the input and output devices, numerical control devices, servo systems, testing feedback devices and machine tools, etc. composition. It is one of the main varieties of CNC machine tools to solve most of the mechanical parts of the automated processing problems become the most important mechanical processing equipment, CNC machine tools occupy a very important position, for decades has been the world's attention and get The rapid development.
The servo drive system of the CNC machine is divided into two types: the closed loop and the open loop according to the presence or absence of the feedback detection unit. The basic composition of the two types of servo drive systems is not exactly the same. But no matter what type, the implementation of components and its drive control unit are essential. The effect of the drive control unit is to convert the feed command into the form of the signal required to drive the actuator, and the actuator converts the signal to the corresponding mechanical displacement. For closed-loop servo drive system, it is composed of actuators, drive control unit, comparison control link, feedback detection unit, and machine tools. The feedback detection unit feedbacks the actual position of the work table to the comparison control link, compares the command signal with the feedback signal, and uses the difference between the two as the following error of the servo system to drive the control unit, drives and controls the execution The element drives the table movement. In the CNC system, due to the introduction of the computer, the function of the comparison control function is completed by the software, which leads to some changes in the system structure, but basically consists of the implementation element, the feedback detection unit, the comparison control link, the driving control unit and the machine tool.
2. The application of digital industry prospects
High-speed, high-precision processing technology and equipment with the new trend of development, efficiency has become the most fundamental factor in efficiency, we are in the rapid development of manufacturing technology period, CNC system processing accuracy will directly affect the overall processing time.
CNC machine tools on the servo system location accuracy to a large extent determine the CNC machine tool processing accuracy. So position accuracy is an extremely important indicator. CNC machine tool servo system in order to ensure that there is sufficient position accuracy, on the one hand is the correct choice of the system in the open-loop magnification size, on the other hand is the accuracy of the location detection components requirements. Because the servo system in the closed-loop control system is difficult to distinguish between the error of the detection element itself and the deviation of the detected components, the accuracy of the feedback detection element often plays a decisive role in the accuracy of the system. It can be said that CNC machining accuracy is mainly determined by the accuracy of the detection system.
The minimum amount of displacement that the displacement detection system can measure is called resolution. The resolution depends not only on the detection element itself, but also on the resolution or pulse equivalent of the measurement system. The general requirement is one order of magnitude higher than the machining accuracy.
The reliability of the servo system of the CNC machine is one of the main quantitative indexes to evaluate the reliability. It is defined as the probability that the product will complete the specified function under the specified conditions and the specified time. For CNC machine tools, its provisions for the conditions of its environmental conditions, working conditions and working methods, such as temperature, humidity, vibration, power, interference intensity and operating procedures. The function here mainly refers to the use of CNC machine tools, such as CNC machine tools of various functions, servo performance. The average failure time (MTBF) refers to the repairable equipment or system where the repair or replacement parts can continue to work. The average time of the servo system from one fault to the next, As a quantitative indicator of reliability.
CNC machine tool servo system due to the use of computer numerical control device, the reliability greatly improved, so the reliability of the servo system is relatively prominent. Its fault comes mainly from the servo components and mechanical transmission part. In general, the reliability of the hydraulic servo system is worse than that of the electrical servo system. The reliability of the electromagnetic components such as solenoid valves and relays is poor. Instead of using the contactless components. At present, CNC machine tools due to component quality, process conditions and costs and other restrictions, its reliability is not high.
3. The force of Sichuan servo system advantages
1. The high resolution of the servo can effectively meet the high precision requirements of the numerical control system.
2. Servo response bandwidth wide range, can effectively adapt to the NC system load changes and rapid response requirements.
3. Servo provides a wealth of parameter settings, by setting the electronic gear ratio, frequency coefficient, S-curve, gain filter parameters can be effective with the host computer system to complete processing.
4. Servo low-speed steady-state high precision, wide speed range, can adapt to some special industry requirements for speed.
5. Servo reliability, you can use a variety of harsh environments, effectively improve system stability and anti-jamming capability.
4. Concluding remarks
The use of force-chuan AC servo CNC lathe can achieve the performance of CNC machine design, the feed shaft with start and stop quickly, smooth operation, improve the cutting accuracy and efficiency of good features.